Badanie szczelności wymienników ciepła
Proces pasteryzacji
Podczas pasteryzacji przez jedną sekcję wymiennika przepływa produkt, który jest ogrzewany parą wodną skraplającą się w drugiej sekcji wymiennika. Energia cieplna zostaje przekazana z pary do produktu za pośrednictwem płyt rozdzielających. Produkt zostaje podgrzany do odpowiedniej temperatury i na odpowiedni czas. Parametry te są związane z technologią produkcji i zależą od rodzaju produktu. Zużyta para jest odprowadzana z układu jako kondensat.
Jeżeli proces tego wymaga to pasteryzowany produkt zostaje schłodzony przez zimną wodę w trzeciej sekcji. Analogicznie jak w procesie podgrzewania ciepło jest przekazywane przez płyty z produktu do wody chłodzącej. Na tym etapie nie jest ważny czas. Istotna jest natomiast temperatura wyjściowa produktu. Zależy ona od tego jaki jest następny etap w procesie i jego warunków prawidłowego wykonania. Z układu odprowadzona jest woda ogrzana.
Na tym etapie pracy produkt jest zabezpieczony w taki sposób, że jego ciśnienie jest wyższe od ciśnienia pary i wody chłodzącej. W przypadku nieszczelności to produkt ma się dostać do mediów, a nie odwrotnie. Zasada ta działa kiedy program sterujący przepływem jest odpowiednio starannie napisany i cały czas pilnuje odpowiedniej różnicy ciśnień.
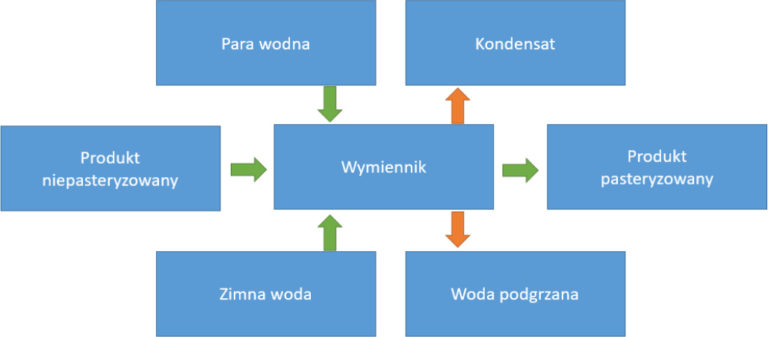
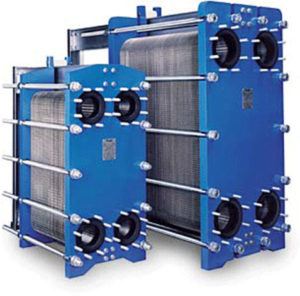
Mechaniczne zagrożenia produktu
Produkt przepływając przez pasteryzator musi mieć fizyczny kontakt z płytami wymiennika. Oznacza to, że jakość i czystość powierzchni płyt ma bezpośredni wpływ na jakość produktu. Pozostawienie niedomytego pasteryzatora z resztkami produktu lub osadzenie się kamienia, grozi oderwaniem i zanieczyszczeniem produktu.
Kiedy dochodzi do mikropęknięć płyt wymiennika to pojawia się miejsce, w którym mogą się nagromadzić zanieczyszczenia stałe. Zwiększa to ryzyko dla produktu. Kiedy mikropęknięcia powiększają się i powstaje nieszczelność to ryzyko wzrasta. Każde zanieczyszczenie mechaniczne może się gromadzić w szczelinie i może zostać wymyte przez produkt.
Układy parowe zwykle są zanieczyszczone drobinami związków żelaza pochodzącymi z korozji armatury. Nie to duże ilości ponieważ woda pracująca w obiegu zamkniętym jest pozbawiona tlenu. Jednak te zanieczyszczenia, które się wytworzyły są tak drobne, że mogą się przedostać przez większe nieszczelności.
Układy wody chłodzącej są większym problemem ponieważ woda technologiczna, która nie jest demineralizowana może pozostawiać kamień. Zawiera również więcej rozpuszczonych gazów, w tym tlenu. Ułatwia to powstawanie korozji w armaturze. Wymusza to założenie, że woda to może posiadać duże ilości zanieczyszczeń stałych o różnym składzie. Jest to jeden z powodów, dla których należy regularnie sprawdzać wymiennik pod względem szczelności. W przypadku długiego okresu braku kontroli może dojść do wypracowania uszczelek i poluzowania połączenia. Daje to nieszczelność tak dużą, że podczas próby ciśnieniowej woda wylewa się na zewnątrz. Jest to zdecydowanie za późno na reakcję.
Jedną z zalet wodorowej metody badania szczelności jest to, że nieszczelność można wykryć jeszcze przed jej wystąpieniem. Daje to dużo czasu na zaplanowanie i podjęcie działań naprawczych.
Chemiczne zagrożenia produktu
W procesie technologicznym produkt ciągle znajduje się w pobliżu pomocniczych substancji chemicznych. Są to zwykle środki myjące, dezynfekujące, oleje, smary i inne. W czasie pasteryzacji w przepływie normalnie nie ma zagrożenia kontaktu z tymi środkami.
Jednak technologia wymaga, aby układ myć przy zmianie produktu oraz co pewien okres czasu. Obecnie ogólnie stosowane są metody CIP (Cleaning In Place) czyli mycie wnętrza rur jak i wymienników bez demontażu. Służą do tego środki zarówno kwasowe jak i zasadowe. Mają one na celu zmyć z powierzchni armatury resztki produktu, wytrąconego tłuszczu oraz kamienia. Dodatkowo dezynfekują układ.
Także i w tym przypadku prawidłowo utrzymany wymiennik nie sprawia zagrożenia dla produktu. Jednak nieszczelności mogą być miejscem magazynowania resztek środków, które będą się przedostawały do produktu. Dużym zagrożeniem może być przedostanie się wody technologicznej do produktu. Woda ta nie może być uważana za czystą i bezpieczną. Zwykle jest tylko częściowo oczyszczona, a jej obieg nie jest sterylny. Armatura wody nie jest objęta procedurą czyszczenia CIP.
Biologiczne zagrożenia produktu
Biologiczne zagrożenia są najpoważniejszym problemem w przemyśle spożywczym. Zakażenie produktu może się ujawnić nawet po miesiącu, a źródło zakażenia jest bardzo trudne do zlokalizowania.
Walka z bakteriami, których źródła nie można odszukać kończy się rozebraniem i dezynfekcją całej instalacji krok po kroku. Wykonuje się też ogromną ilość badań mikrobiologicznych. W przypadkach ekstremalnych linia produkcyjna może być bardzo długo zatrzymana.
W przypadku braku usunięcia problemu istnieje ryzyko wycofania całej instalacji z produkcji. Dla mniejszych zakładów to zwykle oznacza bankructwo.
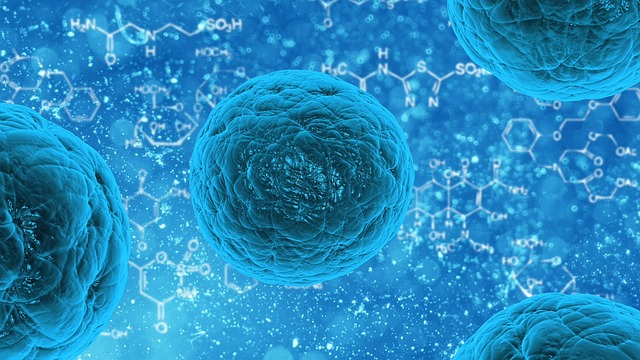
Tak jak w przypadku zagrożeń mechanicznych i chemicznych mikropęknięcia w płytach wymiennika mogą magazynować kultury bakterii. Tu jednak problem jest zdecydowanie poważniejszy ponieważ film bakteryjny potrafi być bardzo trwały. Często bardzo trudno jest go usunąć z płaskiej powierzchni. Wymycie go ze szczeliny może być wręcz niemożliwe.
Oczywiście większość pospolicie występujących bakterii ginie w procesie pasteryzacji jednak znane są też mikroorganizmy, które są w stanie przeżyć takie warunki. Jeżeli pojawiają się w danym zakładzie to spędzają sen z powiek całej kadrze bo walka z nimi jest wyjątkowo trudna. Tu regularnie przeprowadzane badanie szczelności metodą wodorową może znacznie zmniejszyć ryzyko zakażenia samego wymiennika.
Metody badania szczelności
Metoda badania szczelności wodą
Polega na napełnieniu badanej sekcji wodą, podniesienia ciśnienia do poziomu testowego. Następnie czeka się przez zadany czas i sprawdza spadek ciśnienia. Zaletą jest prostota i brak potrzeby demontażu. Wad jest więcej. Cały układ musi być bardzo dobrze odpowietrzony, przy dużych wymiennikach ilość wody potrzebnej do badania jest duża. Wszystkie sekcje mają kontakt z wodą technologiczną, która może wprowadzić zanieczyszczenia. Wykrywane są dopiero dosyć duże nieszczelności. Wymiennik powinien być wyremontowany natychmiast. Jest to metoda inspekcyjna, a nie prewencyjna.
Metoda badania szczelności metodą wodorową
Jest to nowoczesna metoda badania szczelności, która nie wymaga demontażu wymiennika. Jest metodą najmniej inwazyjną. Stosowana mieszanka azotu i wodoru jest obojętna chemicznie i jest sterylna. Posiada dopuszczenie do kontaktu z żywnością.
Jest to najbezpieczniejsza metoda ponieważ nie niesie ryzyka dla produktu. Jest również najbezpieczniejsza dla personelu ponieważ nie wymaga wysokich ciśnień. Mieszanka gazowa składa się w 90% z azotu i 10% z wodoru. W tych proporcjach nie niesie ze sobą zagrożenia wybuchem czy zapłonem. Jest bezpieczna również dla wyposażenia ponieważ nie powoduje korozji.
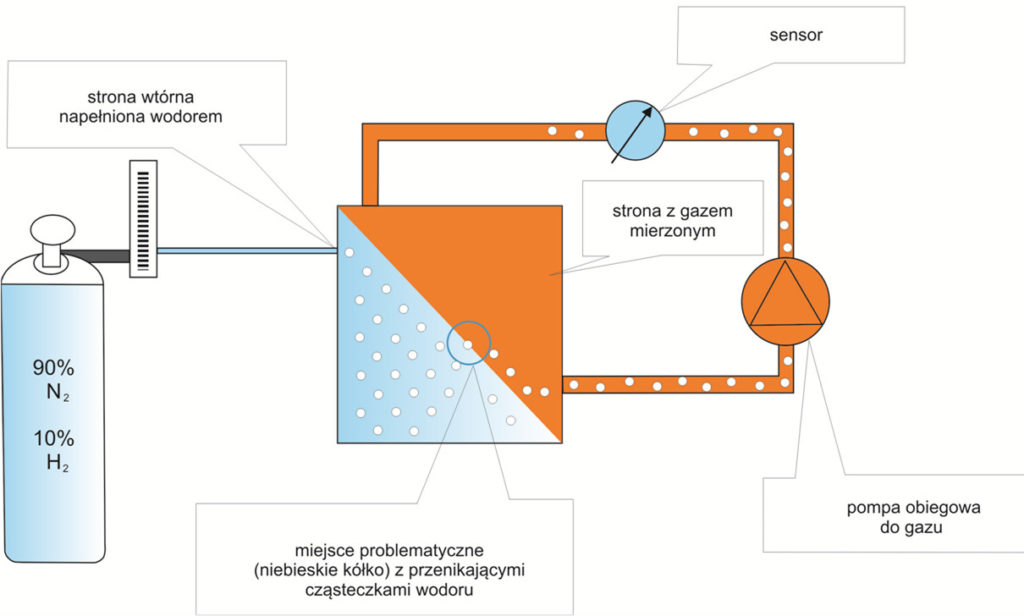
Badanie szczelności metodą wodorową jest najdokładniejsze. Dzięki unikatowym właściwościom wodoru uzyskiwane efekty są najlepsze. Wodór jest pierwiastkiem o liczbie atomowej 1. Oznacza to, że nie ma mniejszego atomu w znanym nam świecie. Jądro atomowe jest zbudowane tylko z jednego protonu. Wokół niego krąży tylko jeden elektron. W przyrodzie występuje w postaci cząsteczek dwuatomowych. Jednak nawet w takiej postaci jest mniejszy nisz pojedynczy atom helu. Tak małe cząsteczki sprawiają, że lepkość wodoru jako płynu jest bardzo niska. Połączenie tych dwóch właściwości sprawia, że jest to gaz niesamowicie przenikliwy. Potrafi wyciec najmniejszą nawet szczeliną. Zbadano również, że może wnikać w powierzchnie metali. Sprawia to, że może przeniknąć przez mikropęknięcie, które jeszcze nie jest utworzone przez całą grubość materiału. Otrzymujemy wówczas sygnał, że coś się zaczyna dziać i trzeba planować naprawę. W powietrzu występuje w tak małych stężeniach, że łatwo wykryć najmniejsze przecieki jako przekroczenia normy. To bardzo pomaga w utrzymaniu wysokiej czułości.
Badanie szczelności metodą wodorową stanowi również działanie prewencyjne. Regularne kontrole dają pewność, że wykryjemy nieszczelność na długo przed wystąpieniem poważniejszej awarii. Daje to czas na zaplanowanie przestoju naprawczego i zamówienie niezbędnych części. Posiadamy więcej czasu na zorganizowanie pracy. Jest to szczególnie ważne gdy korzystamy z outsourcingu i konieczne jest ustalenie dostępnego terminu prac serwisu.
Korzyści wynikające z kontroli szczelności metodą wodorową:
- Bezpieczeństwo produktu
- Czułość
- Szybka, prewencyjna metoda
- Brak konieczności demontażu wymiennika
- Czystość
- Szybkość
- Brak wysokiego ciśnienia podczas badania
- Obojętność gazu