API Schmidt-Brettens’ evaporization systems with SIGMASTAR® Climbing-film Plate Evaporators are used in the food industry, in the organic and chemical industry, and for wastewater treatment.
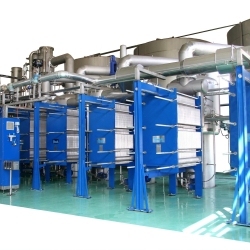
SIGMASTAR®-Evaporization System
Advantages of the rising-film SIGMASTAR® include:
- Superior product distribution due to the thermo-siphon principle.
- Extremely short residence time, to guarantee a gentle treatment of the product.
- Low pressure losses across the tubes, a benefit of the short tube length.
- High concentrations and viscosities are possible due to the high vapor velocity in a rising film.
- Clearly defined product flow path. There is no chance of local over-concentration.
- Lower cost heat transfer area, compared to other evaporation systems.
- No components are welded to the plate surface that can cause corrosion and build up of fibrous materials.
- Flexible design. Capacity changes can be made easily by adding or removing plates.
The unique construction of the SIGMASTAR® evaporization plates makes it possible to apply SIGMASTAR® in a number of different evaporization processes. With problem products (e.g. viscous streams, slurries, and liquids with fouling tendencies) which cannot be processed with falling film evaporators, the SIGMASTAR® evaporizer performs especially smoothly and successfully.
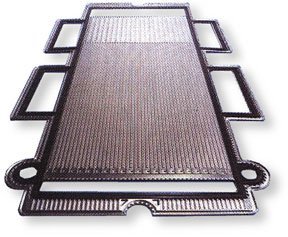
SIGMASTAR® 90V product plate
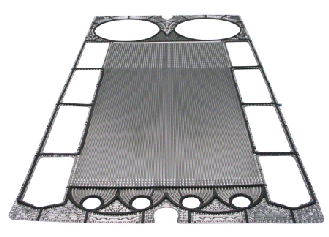
SIGMASTAR® 150V steam plate
Each of these pressed plates is approximately 0,9 m wide, 1,8 m high with longitudinal, sinus form corrugations, which extend over the full width of the plate. The flow passages on the plates are sealed by gaskets held in place by adhesive. This construction has several technical advantages. | ||
Process Description: |
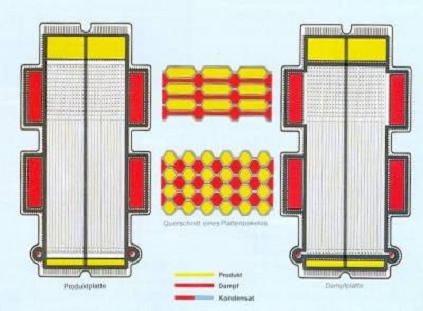
Looking at two plates, aligned in such a way that the projecting points touch, vertical channels are formed which are almost circular and can be considered as “pseudo” tubes. This construction combines the advantages of plates and tubes. The lower part of the plate serves to distribute the liquid to every tubular channel. Steam condenses on one side of the plate, while the product boils on the other. The vapors generated in the tubular channels create a thin, high-velocity film, which rises to the top of the plate. As product boils and rises in the tube, fresh product automatically rises to refill the tube. This distribution technique operates independently of the feed rate and allows a high degree of flexibility.
Due to the special design of the upper part of the heat transfer surface, the heating steam is distributed evenly over the complete width of the plate. The cross-sectional flow area is the same on both sides of the plate, which ensures a well balanced feed into the heating channels.
The illustration above shows a variation of the SIGMASTAR®-90V plate. The SIGMASTAR®-45V plate has an additional gasket down the center of the plate, which allows two products to be processed simultaneously. A product plate is shown on the left illustration in figure A. On the right is the correspondingly partitioned steam plate. Steam can enter either the left, the right or both sides of the plate and the condensate exits from the bottom of the corresponding side of the plate.
The SIGMASTAR®-90V and the SIGMASTAR®-45V can be combined in many different ways to increase the flexibility of our systems, especially for small duties. As the dimensions of both plates are identical, the same frame supports can be used. Expansions and modifications involving both plate types are possible at any time.