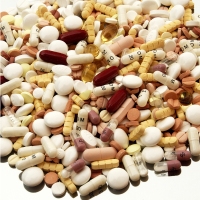
Typical tasks for SIGMA plate heat exchanger in the chemical industries are:
- Thermal processing of infusion solutions
- Cooling of suspensions
- Cooling of tensides
- Cooling and heating of WFI and high-purity water
- Cooling of donor blood and plasma
- Condensation of solvents from production boilers
- Cooling and heating tasks with heat-transfer oils for batch and mix containers
- Thermal processing of ethereal oils
- Cooling and heating tasks for shampoos, shower gels, softeners and liquid detergents
- Consistent system separation of media in special safety heat exchangers
Application example: Cooling and heating of containers
An international pharmaceuticals group headquartered in West Germany has relied for over 10 years on the high quality of the fully-welded plate SIGMAWIG plate heat exchangers of the in all sizes ranging from 2 to 50m² exchange surface. With an order for various units at the end of 2007, we could deliver the 65th SIGMAWIG plate heat exchanger to this customer.
Application example: Drugs
A well-known pharmaceutical company in Frankfurt am Main produces a long-term-effective insulin preparation for lowering blood sugar levels. The active ingredient insulin, which is manufactured in powder form in an adjacent active-substance production plant, is processed in the manufacture, brought into liquid form and filled into an injection ampoule for injection. API Schmidt-Bretten has supplied several plate heat exchangers, including also a SIGMA unit, with which a storage tank is cooled, where the exothermic heat in the amount of >2,000 kW is carried off directly. The equipment has a heat exchanger surface of >200 m² . The project planning of this central cooler unit was implemented using an internationally active contractor.
Application example: Detergent production
A manufacturer which produces (among other things) liquid detergents. In the production process, exothermic heat is generated in batch operation. This must be carried off before the filling of the detergent. For that, a SIGMA plate heat exchanger with an exchange surface of 200 m² was brought into operation for the first filling line. The product is cooled in the cooler from 60°C to a filling temperature of < 35°C. The liquid detergent can indicate a dynamic viscosity of to 3,750 cP, according to temperature. The equipment provides the required performance to the satisfaction of the customer. Following this, a further cooler with the same layout was ordered for a second filling line.