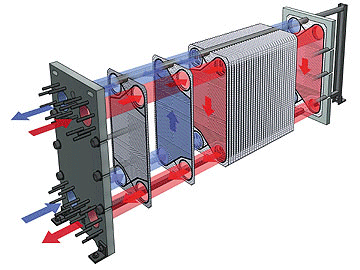
The special design of a plate heat exchanger makes it possible to create individual arrangements with a variety of heat exchange plates. Each plate with its own design patterns, thermal and pressure loss properties, is arranged in such a way that a specific product undergoes the thermal process under optimum conditions.
Plate heat exchangers consist of a number of single plates which have predetermined dimensions. The choice of the plate corrugation influences the hydraulic as well as the thermal functioning of the plate heat exchanger. The variations between the different corrugation designs consist mainly of a change in angle of the ribs or in the groove height. The thermodynamic properties of a single plate heat exchanger can be optimised through the rearranging of the plates, resulting in a redirecting of the products’ flow pattern within the unit.
The special design of a plate heat exchanger makes it possible to create individual arrangements with a variety of heat exchange plates. Each plate with its own design patterns, thermal and pressure loss properties, is arranged in such a way that a specific product undergoes the thermal process under optimum conditions.
Plate heat exchangers consist of a number of single plates which have predetermined dimensions. The choice of the plate corrugation influences the hydraulic as well as the thermal functioning of the plate heat exchanger. The variations between the different corrugation designs consist mainly of a change in angle of the ribs or in the groove height. The thermodynamic properties of a single plate heat exchanger can be optimised through the rearranging of the plates, resulting in a redirecting of the products’ flow pattern within the unit.
Circuit variations are mainly created through the parallel connection of flow channels within a connecting passage and the series switch from several connecting passages. The products’ flow path generally follows a counter directional path, this means that the products which are taking part in the thermodynamic process flow in opposite directions. The advantage of this counter flow principle in contrast to the parallel flow principle, in which the two mediums flow into the same direction, is that a temperature intersection is possible. This temperature intersection is created when the exit temperature of the hot medium is lower than the exit temperature of the cold medium.
Parallel Connection
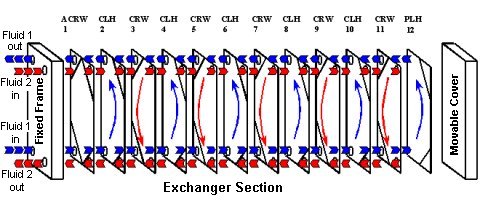
The construction of a plate heat exchanger makes it possible to arrange plates with different corrugation patterns, and with different thermodynamic as well as pressure loss properties, in such a way that the product can be treated under the optimum conditions. In general all the connections of a plate heat exchanger (PHE) enter through the fixed frame plate. This construction avoids the necessity of having to dismantle any connecting pipes when the plate heat exchanger is opened for cleaning or servicing. The optimising of the plate heat exchangers thermodynamic characteristics is achieved through the parallel product flow past a variety of plate corrugations.
With this connecting system the product flows through the installation only once during its dwell time. Because the thermal length of a set of heat exchange plates can only be used once within a thermal process. It is recommended to use one of the two following options to optimise the process. One option is to add more heat exchange plates to the plate heat exchanger, the other would be to incorporate plates with different corrugation patterns i.e. flow patterns.
The combination of different plate corrugations within the plate arrangement (block arrangement) allows to optimise the characteristic of the PHE. Variing the number of each type of channel in parallel arrangement leads to a wide range of thermal and hydraulic behaviour.
Within a block connection two different types of heat exchange plates with different corrugation patterns, hydraulic, as well as thermodynamic properties are used in parallel connection.
When the product is pumped through the block connection containing different types of plates, gaps with varying flow resistance are created, resulting in a varying product flow speed. Due to this reason block connections should only be used with “clean” products, in order to avoid the creation of fouling zones within the heat exchanger.
Circuit Switch
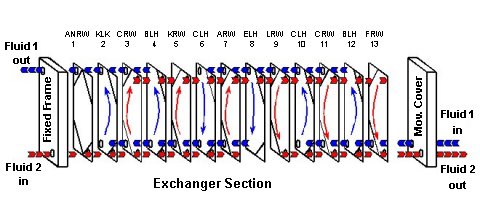
Enlargement of the thermal process length through counter flow path serial connections within the connecting passages.In certain cases the standard size of a plate heat exchanger is not large enough to accommodate the thermal length required for the processing of certain products.
In order to enlarge the thermal process length and improve the thermal transfer process the option exists that a number of connecting passages are redirected through a frame.
Through the rearrangement of the of the connecting passages into a series, a counter flow circuit is created. This counter flow circuit is produced because one of the mediums enters the plate heat exchanger through the first connecting passage and then exits the plate heat exchanger after passing through the last connecting passage. The other liquid, in contrast enters through the last connecting passage and leaves the plate heat exchanger through the first connecting passage.
The circuit switch makes it possible to attain high heat transfer as well as a high k-values even with small volume flows in small plate heat exchanger models.
In order to optimise the circuit switch, single connecting passages may be equipped with a variety of plates with different corrugation patterns, hydraulic as well as thermal properties.
In this manner it is possible to adapt the plate heat exchanger to a variety of products, an option which is especially useful for fluids changing their properties during the thermal process and also shear-sensitive fluids.