Hydrogen leak detection for heat exchangers
Pasteurisation process
During pasteurisation process, a product flows through one section of the exchanger, which is heated by steam condensing in the other section of the exchanger. Thermal energy is transferred from the steam to the product via separating plates. The product is heated to the right temperature and for the right time. These parameters are related to the production technology and depend on the type of product. The used steam is discharged from the system as condensate.
If the process requires it, the pasteurized product is cooled by cold water in the third section. Similarly to the heating process, heat is transferred through the panels from the product to the cooling water. Time is not important at this stage. The output temperature of the product is important. It depends on what is the next stage in the process and its conditions for proper implementation. Heated water is drained from the system.
At this stage of operation, the product is protected in such a way that its pressure is higher than the pressure of steam and cooling water. In the event of a leak, the product should enter the media, not the other way around. This principle works when the flow control program is properly written and constantly monitors the appropriate pressure difference.
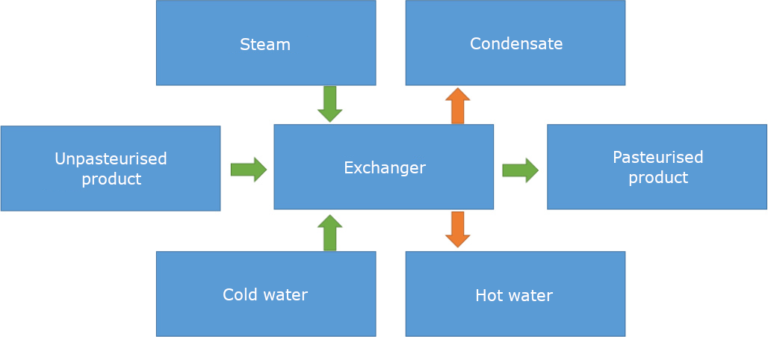
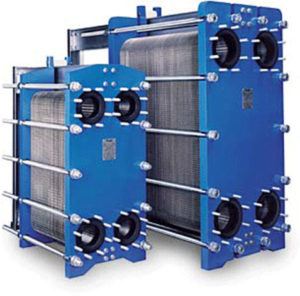
Mechanical product hazards
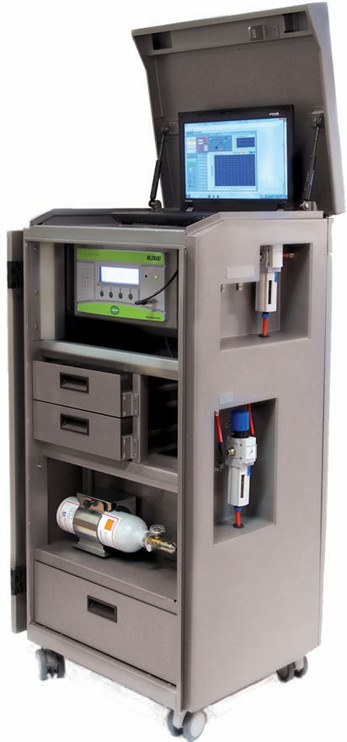
Leak detection HLD 600 automatic
The product flowing through the pasteurizer must have physical contact with the heat exchanger plates. This means that the quality and cleanliness of the surface of the boards has a direct impact on the quality of the product. Leaving the unpasteurized pasteurizer with product residue or limescale build-up may cause detachment and contamination of the product.
When the microcracks of the exchanger plates occur, a place appears where solid impurities can accumulate. This increases the risk to the product. When the microcracks increase and a leak occurs, the risk increases. Any mechanical contamination can accumulate in the gap and can be washed away by the product.
Steam systems are usually contaminated with particles of iron compounds from the corrosion of fittings. This is not a large amount because the water working in a closed circuit is deprived of oxygen. However, the impurities that have formed are so fine that they can penetrate larger leaks.
Cooling water systems are a bigger problem because process water that is not demineralized can leave scale. It also contains more dissolved gases, including oxygen. This facilitates the formation of corrosion in the fittings. This forces the assumption that this water may have large amounts of solid impurities of varying composition. This is one of the reasons why the exchanger should be checked regularly for leaks. In the event of a long period of inaccessibility, seals may form and loose the connection. This gives a leak so great that during the pressure test water spills out. It’s too late to react.
One of the advantages of the hydrogen leak test method is that the leak can be detected before it occurs. This gives you plenty of time to plan and take corrective action.
Chemical product hazards
In the technological process, the product is still close to auxiliary chemicals. These are usually cleaning and disinfecting agents, oils, greases and others. During pasteurisation in flow, there is normally no risk of contact with these agents.
However, technology requires that the system be washed when the product changes and from time to time. Currently, CIP (Cleaning In Place) methods are generally used, i.e. washing the inside of pipes and exchangers without disassembly. Both acid and alkaline agents are used for this. They are designed to wash away product residues, precipitated fat and scale from the surface of the fittings. In addition, they disinfect the system.
Also in this case a properly maintained exchanger does not pose a threat to the product. However, leaks can be a place to store leftovers that will get into the product. The process water entering the product may pose a big threat. This water can not be considered clean and safe. It is usually only partially purified and its circulation is not sterile. Water fittings are not covered by the CIP cleaning procedure.
Biological product hazards
Biological hazards are the most serious problem in the food industry. Infection of the product may appear even after a month, and the source of infection is very difficult to locate.
The fight against bacteria whose source cannot be found ends with the dismantling and disinfection of the entire installation step by step. A huge amount of microbiological tests are also carried out. In extreme cases, the production line can be stopped for a very long time.
If the problem is not resolved, there is a risk that the entire installation may be decommissioned. For smaller plants, this usually means bankruptcy.
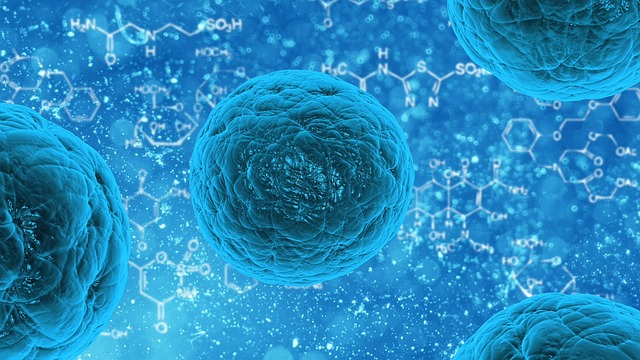
As with mechanical and chemical hazards, microcracks in the exchanger plates can store bacterial cultures. Here, however, the problem is definitely more serious because the bacterial film can be very durable. It is often very difficult to remove it from a flat surface. It may not be possible to wash it out of the gap.
Of course, most common bacteria are killed in the pasteurization process, but microorganisms are also known to survive such conditions. If they appear in a given plant, they spend the night in their eyes because the fight with them is extremely difficult. Regular hydrogen leakage testing here can significantly reduce the risk of contamination of the exchanger itself.
Leak testing methods
Water leaking test method
It consists in filling the tested section with water, raising the pressure to the test level. Then wait for the set time and check the pressure drop. The advantage is simplicity and no need for disassembly. There are more disadvantages. The whole system must be well vented, with large exchangers the amount of water needed for the test is large. All sections are in contact with process water that may introduce contamination. Only quite large leaks are detected. The exchanger should be renovated immediately. This is an inspection method, not a preventive one.
Hydrogen leak test method
It is a modern method of leak testing, which does not require disassembly of the exchanger. Is the least invasive method. The mixture of nitrogen and hydrogen used is chemically inert and sterile. Has approval for contact with food.
This is the safest method because it carries no risk for the product. It is also the safest for personnel because it does not require high pressure. The gas mixture consists of 90% nitrogen and 10% hydrogen. In these proportions there is no risk of explosion or ignition. It is also safe for equipment because it does not cause corrosion.
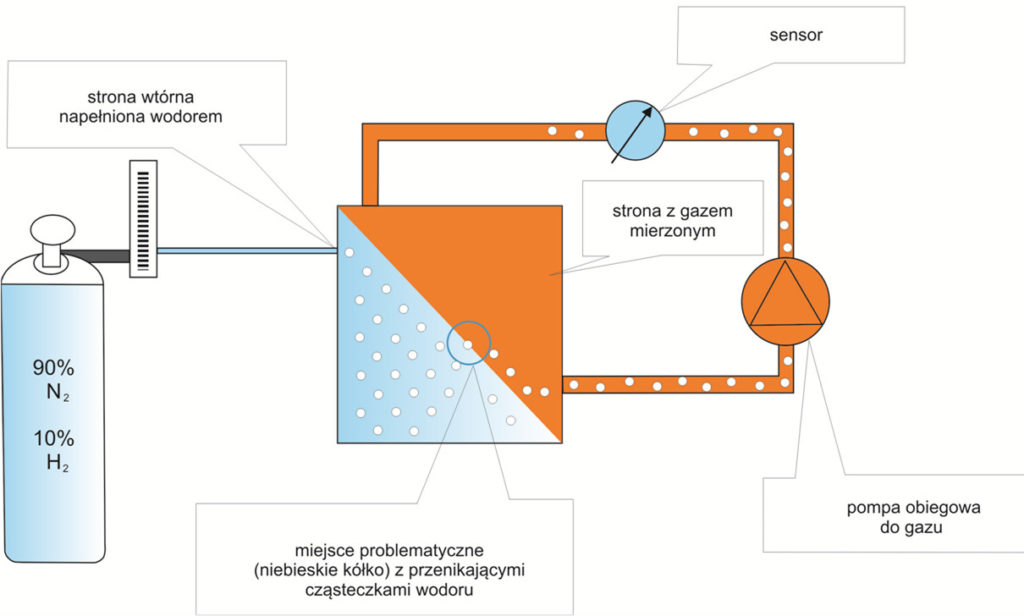
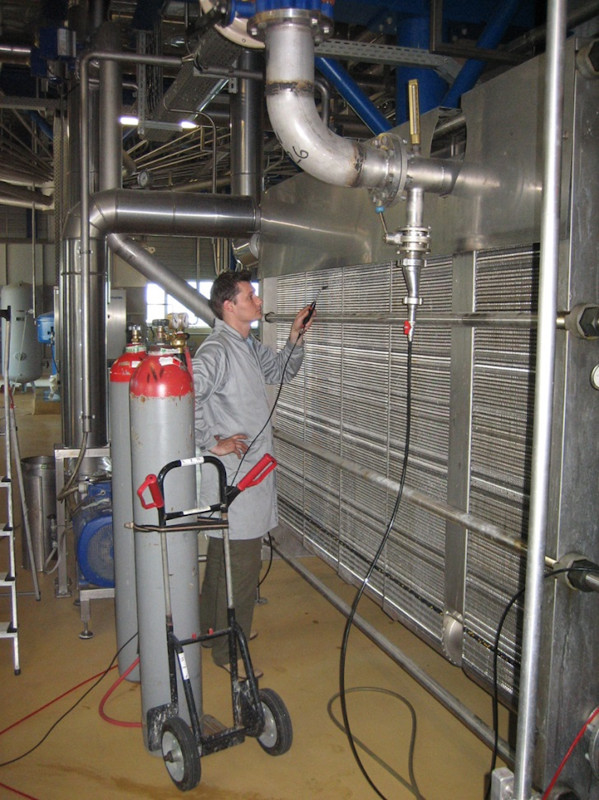
The hydrogen leak test is the most accurate. The effects obtained are the best thanks to the unique properties of hydrogen. Hydrogen is the element with atomic number 1. It means that there is no smaller atom in the world we know. The atomic nucleus is made of only one proton. Only one electron orbits around him. In nature, it occurs in the form of diatomic molecules. However, even in this form there is a smaller niche single helium atom. Such small particles mean that the viscosity of hydrogen as a liquid is very low.
The combination of these two properties makes it an extremely penetrating gas. It can leak even the smallest gap. It was also investigated that it can penetrate metal surfaces. This means that it can penetrate through the micro-crack, which is not yet formed by the entire thickness of the material. Then we receive a signal that something is starting to happen and you need to plan a repair. In air it is present in such low concentrations that it is easy to detect the smallest leaks as exceeding the norm. This helps to maintain high sensitivity. Hydrogen leak testing is also a preventive measure. Regular checks ensure that we detect leaks long before a major accident occurs. This gives you time to plan your downtime and order the necessary parts. We have more time to organize work. This is especially important when we use outsourcing and it is necessary to determine the available date of service work.