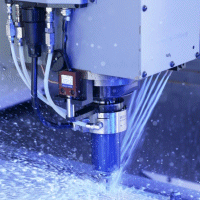
The cooling and tempering of different media (grinding and cutting oils, emulsions, cooling water, hydraulic oils) in the area of the metal processing are among the main applications of SIGMA plate heat exchangers.
In modern, high-precision cutting and grinding centers, the required and unchangeable precision can be achieved on the highest level only if the employed cutting and grinding oils indicate only very slight deviation from the set-adjusted cooling temperature.
This is achieved through cooling systems where the plate heat exchangers, as a main component, are able to carry off the entire heat from the cutting and grinding oils which is generated by all employed system aggregates and the frictional heat arising in the processing, with the aid of optimally coordinated coolants.
Different emulsions, with more or less milk-like consistency, take over important tasks such as acting as cooling and lubricating materials in boring machines, as well as shaping and planing machines. In order to enable this and to keep the tolerance range of the workpieces to be processed as low as possible, plate heat exchangers with their high levels of efficiency and taking up the smallest possible space, guarantee cooling to the specified temperature level.There is also the possibility to link the plate heat exchanger into the so-called bypass mode, according to the structure of the entire cooling system (central emulsion supply or decentralized individual supply), and thus ensure that exact tempering is provided for the entire emulsion stock. In case of thermal processing of workpieces in the metal construction, quenching baths are frequently employed, which are filled with either oil or water. Since the heat generation, according to size and throughput quantity of the workpieces, is mostly higher than the bath is capable of absorbing through natural convection, a forced cooling of the bath content is also necessary here. | ||
Typical tasks for SIGMA plate heat exchanger in metal processing are:
| ||
Application example: Nickel-plating of small partsIn the case of a company in the Duesseldorf area, nickel-plated, mirror-bright cold strips are processed. Finished products, such as battery wrappers or semi-finished products for the electric industry, as well as household and office products, are then manufactured from these. The company has for years had the different nickel lines, which are used for the galvanic surface refinement, equipped with plate heat exchangers from API Schmidt-Bretten. In the different manufacturing plants, SIGMA equipment is used mainly for the heating and cooling of the nickel electrolyte baths. Titanium is generally used as a plate material and EPDM is used as a sealing material. Application example: Manufacture of piston ringsAn internationally active supplier of piston rings for the automotive industry, with different production works in Germany, has employed screw-connected plate heat exchangers for more than 20 years in production. The well-proved SIGMA plate heat exchangers are used especially for the cooling of galvanic baths in the manufacture of these piston rings. These are generally equipped with plates of titanium and seals of Viton. More than 150 equipment units have been installed in the production works in Germany. In production plants abroad at least 50 equipment units have been installed. |