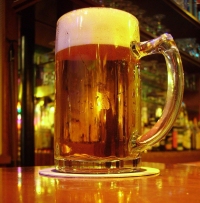
In breweries the plate heat exchanger has been used as standard technical equipment since the introduction of the closed wort routing (a successor of the surface irrigation cooler). Over the years the applications have grown extensively.
Plate heat exchangers are also employed today in breweries for exhaust vapor condensation, yeast cooling, beer deep-freezing, heating of CIP solutions and other thermal procedures.
A classical example of the use of the plate heat exchanger is short-term heating for the thermal stabilization of beer and non-alcoholic drinks.
Typical tasks for SIGMA plate heat exchanger in the brewing industry are:
- Cooling and heating of wort
- Cooling of yeast
- Exhaust vapor condensers
- Cooling of condensate
- Hot water boiler
- CIP heater
- De-alcoholization plants
- Concentrate systems for yeast, malt extract and wort
Application example: WORT COOLING
Since the company foundation in 1879, wort cooling has been represented in the standard program of API Schmidt-Bretten. SIGMATHERM wort coolers can be adapted to the respective requirements of mashing liquor:
Traditionally they find application in two-stage implementation or, in accordance with more modern technology, in one-stage implementation with a stacking tank for precooled mashing liquor. The wort aeration is combined in practice with the wort cooling. Exactly-metered air dosing and the finest distribution in the wort guarantee good cold sludge flotation, sufficient oxygen supply of the yeast, and homogeneity of the setting wort.
Application example: WORT HEATER (external cooker)
The purified wort is no longer heated in the pan, as in the pasr, rather it is heated up from the supply flow container over the plate heat exchanger with 8x to 10x the quantity of the pan content. According to system, the wort is heated up from 72/74°C to 98/99°C with water at 101/104°C, so that water at 78/80°C results. This water is stored and employed for sparging for the next broth.