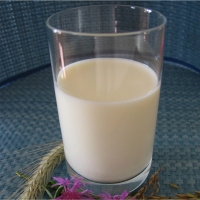
Typical tasks for SIGMA plate heat exchanger in dairy processing are:
- Cooling, heating and short-term heating of milk
- Cooling, heating and short-term heating of yogurt
- Cooling, heating and short-term heating of desserts
- Cooling, heating and short-term heating of ice-cream mixes
- Cooling of curd
- Cooling, heating and short-term heating of cream
- Super-heating of cream
- Cooling of brine
- Hot water boiler
- CIP heater
Application example: MILK PASTURIZER
SIGMA plate heat exchangers have been employed over many decades in order to pasteurize milk using minimal energy. A typical pasturizer consists of three sections. In the regeneration section, the cold milk is warmed up with the aid of the hot, pasteurized milk. Heat recovery of 96% is obtainable without complication. In a further section, the warmed milk is brought to a pasteurization temperature of 72 – 74°C with the aid of hot water.
After the pasteurizing, the milk is routed through the regeneration section to the refrigeration section. Here it is cooled with the aid of ice water to the storage deposition temperature 4°C on average. As a result of the very small temperature differences between the service media and the milk, the milk is handled very gently. These temperature differences are easily achieved with SIGMA heat exchangers.