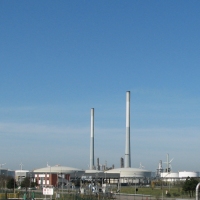
Typical tasks for SIGMA plate heat exchanger in the petrochemical industries are:
- Condensation of solvents and multiple-material mixtures
- Cooling / Heating of reactors and production containers
- Cooling and heating of intermediate products
- Cooling of hydrocarbons
- Cooling of water circuits
- Benzene / Benzene heat recovery
- Heat recovery within petrochemical processes
Application example: Unconverted Oil
For the reheating of 45 t/h of so-called “Unconverted Oil” by means of 2,380 kg/h saturated steam at 4.5 bar, our fully-welded SIGMAWIG plate heat exchangers were installed in a gas scrubbing system of the refinery. For reasons of availability, two units in total were installed as redundant backup.
Application example: Solvents
For the cooling of 76 t/h raw toluene, two plate heat exchangers are installed with an exchange surface of 102 m² each. Due to the pure solvents, special SIGMACOAT PTFE-jacketed seals are used. In a downstream process system, occurring vapor condensate is cooled with two more SIGMA units.
Application example: Quench water
An internationally active plant engineering group has installed a complete ethylene oxide system in a petrochemical plant. In this system, two SIGMA equipment units, with plates in material 1.4547 and seals in Viton G quality, are used for the cooling of the so-called “quench water”. Furthermore, a fully welded SIGMAWIG plate heat exchanger is also operated for the heating of distilled water by means of saturated steam at 170°C.