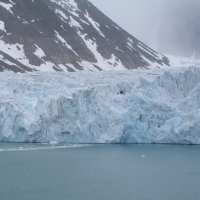
According to energy demand, the coolant oil flows through one or more heat exchangers arranged in parallel. In complex cooling systems, part-flows are diverted from a central circuit according to requirement and, according to work profile, routed to the “refrigeration consumption location” through a local plate heat exchanger.
Typical areas of application of plate heat exchangers in refrigeration cycles are:
- Vaporization of refrigerants
- Condensation of refrigerants
- Employment as economizer
- Cooling of compressor oil
- De-coupling of refrigeration from central refrigeration cycles
- Cooling of cooling circuits
Application example: For NH3 systems
If ammonia is employed as a refrigerant, compact, welded plate heat exchangers can be employed since rubber sealing cannot guarantee 100% leak-tightness of the ammonia circuit. These welded plate heat exchangers are available for small to medium volume flows as fully welded equipment (solid stainless steel pressure frame) under the type designations SIGMAWIG ST 3, ST 12 and ST 18. For example, equipment of the type SIGMAWIG ST 3 is employed in different sizes in tempering devices for test stands in the computer and semi-conductor industry. A significant requirement in this case is a chemically pure and copper-ion-free circulation process, in order to avoid contamination of the component parts, printed circuit boards and printed circuit boards. The equipment units with the designations SIGMAWIG ST 30 and SIGMAWIG ST 40 are suitable for large energy transfer capacities and volume flows, with welded plate package in painted pressure frames.